Pain Point
Scheduling Mess
Lack of scheduling planning for the production process.
Wide range of materials
Material issuing or loading.Wrong material occurs.
Opaque data
Chaos in the workshop, non-transparent management.
Difficult quality management
Product quality is
difficult to trace, low customer trust.
difficult to trace, low customer trust.
Less equipment utilization
The status of the equipment cannot be monitored.
The electronics industry
needs to enhance capacity
Increasing competition in the electronics industry, rising raw materials, increasing labor costs, rising customer requirements and greater focus on product quality and reliability.
In the actual production, enterprises are also faced with complex and changing production forms, and the requirements for the assembly process of electronic products are getting higher and higher. It is necessary to ensure the controllable quality of the products, the speed of delivery information and flexible production, but also requires the continuous innovation of the enterprise\\\'s technology and the transparency of production to adapt to the complex production process.
In the actual production, enterprises are also faced with complex and changing production forms, and the requirements for the assembly process of electronic products are getting higher and higher. It is necessary to ensure the controllable quality of the products, the speed of delivery information and flexible production, but also requires the continuous innovation of the enterprise\\\'s technology and the transparency of production to adapt to the complex production process.
Driven by six core functions
Basic Data Management
Basic data modeling, standardized modeling of material base data, product BOM list, process flow and product layout.
Dynamic Scheduling
It takes into account factors such as materials, workshop capacity, order insertion and withdrawal to ensure maximum plan executability.
Warehouse and Materials Management
Through material bar-coding or RFID management, we can efficiently operate IQC inspection,.etc of materials.
Production process tracking
Effective implementation feedback on the product production process, and real-time monitoring and early warning to ensure the smooth production process.
Full quality control
Provide perfect product whole process quality data, provide reliable data support for product quality traceability and process optimization.
Equipment Resource Management
We can effectively manage the repair and maintenance of production equipment, monitor and count the effective working status and process parameters.
Value
Core Values
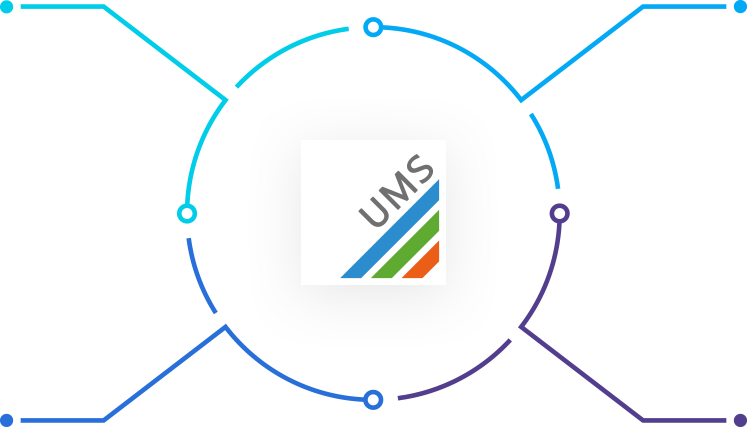
Lean Manufacturing
Efficient scheduling and operation of production resources, minimization of production and operation costs, and lean production management.
Customer Auditing
Easily meet the quality control and supply system auditing requirements of major international manufacturers and greatly increase customer satisfaction.
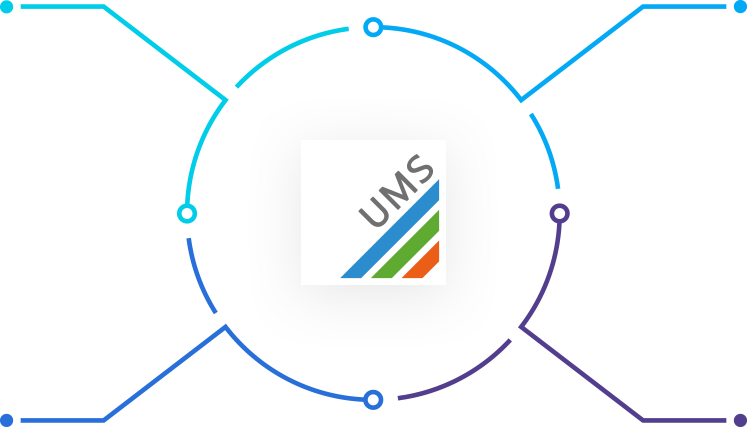
Controlled process
Realize the comprehensive management of digital factory and realize the maximum value of data resource elements.
Transparent Management
Improve the management efficiency of the production plant, from the traditional manual management up to the digital transparent workshop.

UMS
Upgrade
80%
execution
Improve
65%
decision accuracy
Assistance
70%
efficiency
Project Landing Process
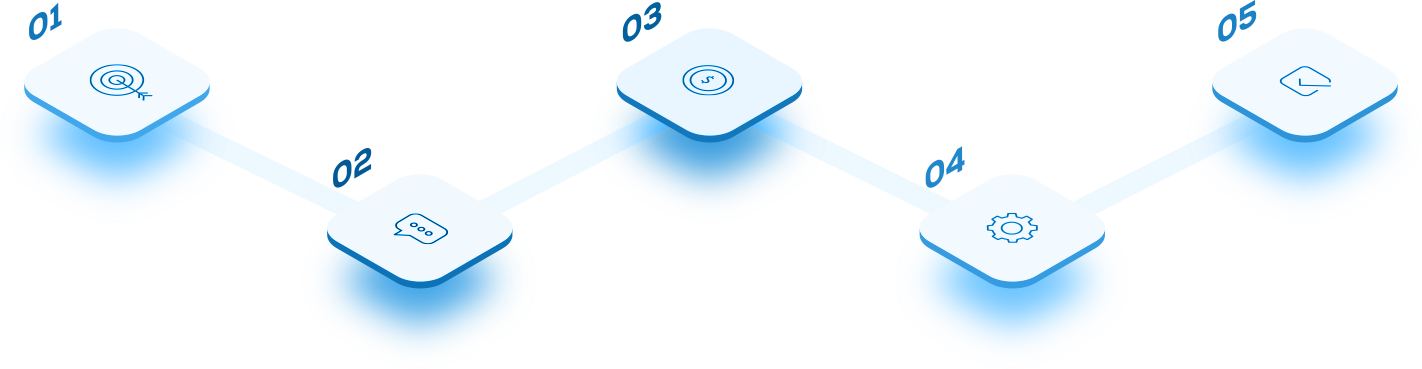
01Business Research & Solution Design
Start the business research of enterprise requirements.
carry out the corresponding solution planning and design
carry out the corresponding solution planning and design
02System Implementation
Depending on the deployment environment.Targeted development and system adaptation.
03Project Implementation
Conduct formal environment deployment.Drive the system online for use.
04System Trial Run
Conducting the trial run of the system before going online.
Performing maintenance on the basic data
Performing maintenance on the basic data
05After-sales support
Provide high assurance after-sales support